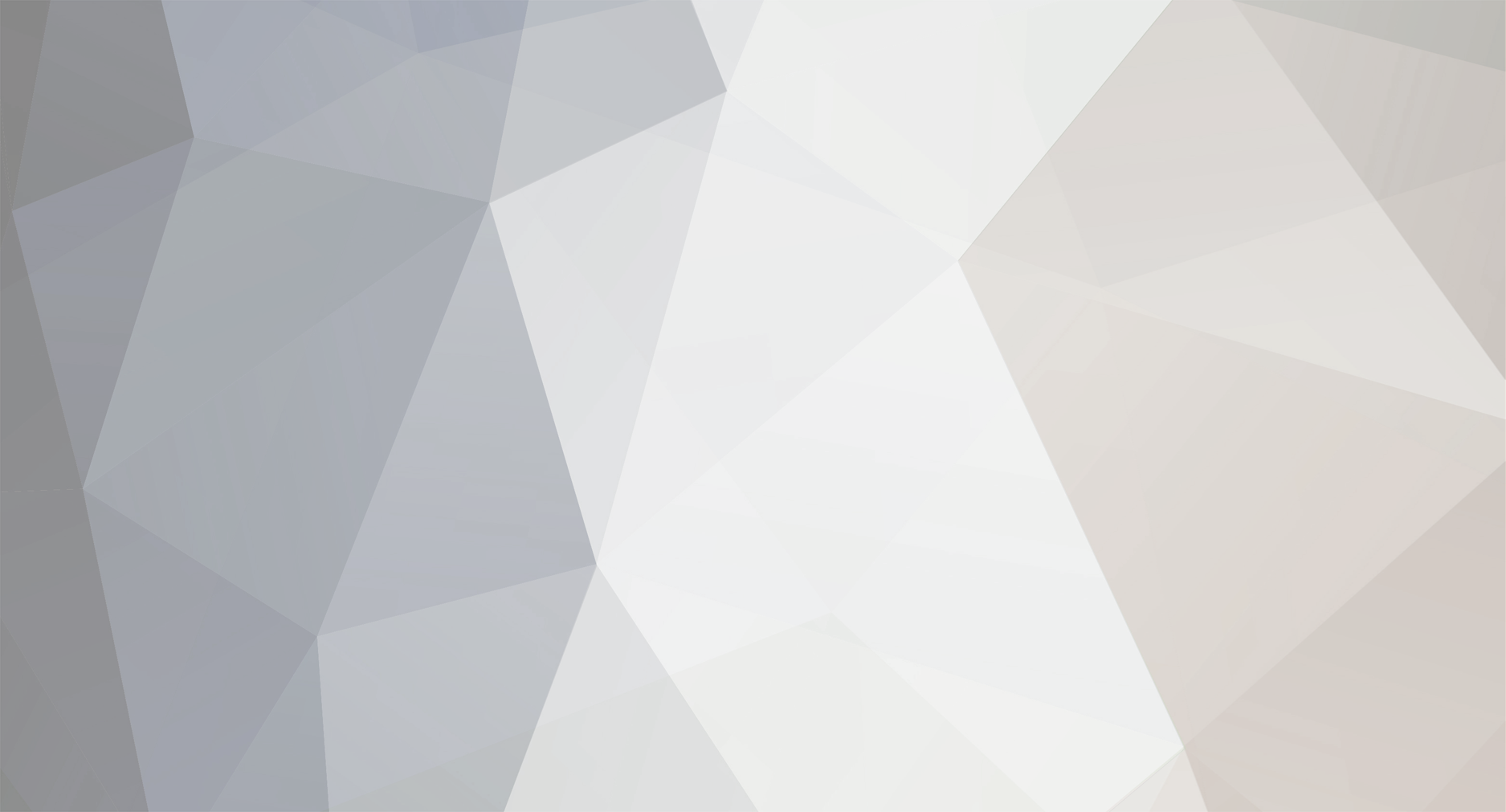
dangonay
LP Member-
Posts
7 -
Joined
-
Last visited
-
For an update on the car and its progress please follow this link. Countach Standalone Conversion We have the drive-by-wire throttles working and the car is ready to start. Should be running this week. Here's a couple pics of the DBW system...
-
Ignition Coils These are BMW M3 ignition coils which were the only ones we could find that were deep enough to fit this engine. Spark plug "tubes" were machined slightly wider at the top to allow the coils to fit. The rubber boot on the coil only required slight trimming to fit. Not much clearance when the manifold is on, but it'll do.
-
Intake Manifold. Shots showing a test fit of the throttle bodies. These are drive-by-wire electronic throttles - no more linkages. Note the o-ring groove to seal the throttle body to the manifold instead of using a gasket. The burn marks are from the coating that was on the stock manifolds. These pics are also before the cold start injector and air bypass fittings were "removed" and before the injector bungs were welded in. Before and after shots of the intake manifold. Test fit of manifold and fuel rails to engine.
-
Fuel rails. Shot of the fuel rail with the injector extensions. The extensions are sealed with o-rings and the rail is drilled with a pocket to accept the o-ring. And here is the nifty little tool that machines the hole in the fuel rail and also the pocket for the o-ring in one pass. You can also see why we needed extensions to connect the fuel injectors to the rails and clear the intake runners. Test fit of fuel pressure sensors. Fuel pressure regulators and mounting bracket. The housings are machined to accept standard Bosch regulators. These are a great product, IMO, and saved a lot of time for us. Regulators mounted to manifold. Like the stock Countach, we are using two fuel pumps - one for each bank. Likewise we have separate fuel rails and regulators for each bank as well.
-
Fuel injectors. The main problem we had with finding injectors is the location and design of the stock injectors. Bosch CIS injectors are very long and narrow. You can see the stock injector takes up very little space inside the runner. If we used standard fuel injectors, we would have had to install an injector bung in the runner and that would have had a significant effect on flow through the runner. We found that Audi used an injector in the TT which had a "snout" on the end of it. This allowed us to move the injector bung much further up the runner and minimize instrusion into the runner. Shot of the injector and the extension used to connect to the fuel rail. The injector bung and injector. The bung had to be tapered to allow the electrical connector enough clearance. The injector bungs welded into the manifold.
-
Next up is the crankshaft position sensor. Steel sleeve pressed into stock crankshaft pulley. Trigger wheel mounted to "sleeve". Completed pulley/trigger wheel on engine. Plastic used as a template for mounting bracket. Studs were installed with red loctite to replace the factory bolts. Completed mounting bracket made from 1/4" aluminum plate. I doubt it's going to flex at all. The mounting holes on the bracket are oversized by 1mm allowing the sensor to be lined up directly over the trigger wheel. Sensor installed into bracket. It's retained by three set screws.
-
We are doing a conversion of a 1988.5 Countach. Vehicle had a few issues (small fire and oil problems). We rebuilt the engine and are now adding an aftermarket fuel injection system. The factory fuel injection system did not work. Both computers were bad and fuel system sat for so long (with water in fuel) that all major parts were ruined. Car is almost complete so here's a bit on its progress. Distributor modified to accept a hall effect cam sensor shutter wheel. Aluminum sleeve was made to allow the mounting of the camshaft position sensor. Note the spring pins in the sleeve used to locate the sensor. The camshaft position sensor (commonly used on Audi V6's). The mounting "ears" have been lopped off. The camshaft sensor mounted to the sleeve. Another shot of the sensor. The distributor housing modified to accept the camshaft position sensor. Hole cut in the side for the electrical connector. Other side of distributor with the camshaft sensor installed. The aluminum "plug" is what holds the sensor in place. Distributor with the hold down plug in place. The completed conversion. A metal cover is placed where the distributor cap used to go. We now have a camshaft sensor inside our modified distributor while still retaining some of the "look" of the original. Test fit showing completed "cam sensor" on the engine.